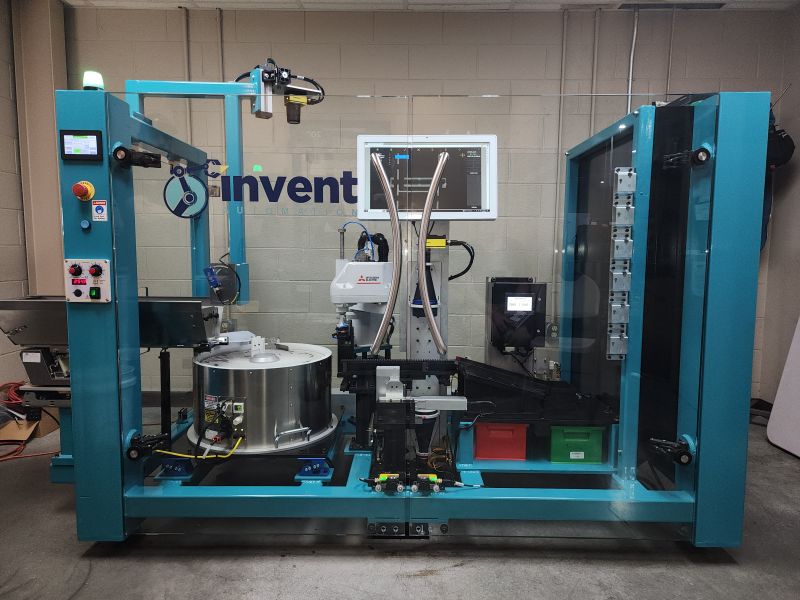
Invent Automation has built-in CapSen imaginative and prescient know-how as DENSO automates. Supply: Invent Automation
Automotive manufacturing has lengthy benefited from the considerate deployment of robotics and automation, and for good purpose. Among the many many complicated manufacturing processes, some will be too troublesome or too tedious to be accomplished safely and effectively by human staff. In consequence, industrial automation applied sciences can add great worth to authentic gear producers and automotive components suppliers alike in some ways. For instance, main international automotive components producer DENSO not too long ago sought to automate a bodily difficult and repetitive tote-handling job.
As an alternative of letting staff proceed to load and unload massive stacks of heavy totes to and from a paint sales space (Determine 1), the firm partnered with CapSen Robotics, which custom-made its 3D imaginative and prescient, movement planning, and management software program to swimsuit the duty.
DENSO additionally partnered with techniques integrator Invent Automation to develop a system that will streamline the method and permit staff to contribute on the plant flooring in additional worthwhile, much less physically-demanding methods. The exercise contributed to DENSO’s broader efforts to enhance human work with automation for improved workforce member and firm efficiency.

Determine 1: Giant, heavy totes crammed with automotive components are carried to and from a paint sales space on a conveyor, the place a cobot picks and place totes as a part of an automatic course of. Supply: Invent Automation
Gone in (beneath) 60 seconds at DENSO
As a part of DENSO’s operations, automotive components are painted with a low gloss, charcoal-colored paint that visually smooths out the floor for a cleaner look whereas additionally serving to to soak up gentle and cut back glare contained in the automobile.
Within the earlier setup, staff stacked six totes stuffed with plastic automotive components onto a conveyor that have been then offered to an operator who would manually take away the components and put them right into a paint sales space station (Determine 2), then pack them again into the totes. An worker would stack or de-stack a tote each 30 seconds, day in and day trip.
This repetitive movement was recognized as an automation alternative, which might liberate workforce members to carry out extra impactful work. Nonetheless, format constraints on the store flooring made conventional types of automation troublesome, resulting in the creation of a compact and versatile system.
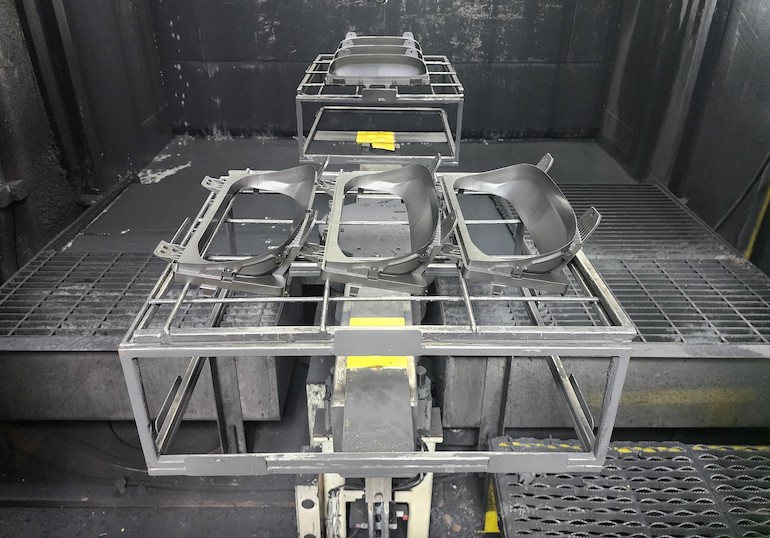
Determine 2: Automotive components are dropped at a paint sales space, the place they’ll be sprayed with a low-gloss paint that smooths out the floor and helps take in gentle contained in the automobile. Supply: Invent Automation
With the brand new system, an inbound conveyor transports totes of unpainted objects to a six-axis collaborative robotic (Determine 3) with an Intel RealSense 3D RGB depth digicam connected to its finish effector. The digicam helps the robotic visually determine the tote and measure its top for choosing.
The CapSen PiC 2.0 software program, operating on an industrial PC with a graphics processing unit (GPU), permits the robotic to plan its movement, find, decide, and manipulate the tote and transfer it towards one other conveyor headed to the paint sales space station. There, the components are unloaded, painted, put into an oven for curing, and inspected earlier than being put again into the totes and onto the conveyor going again towards the robotic, which identifies the tote and locations it onto an outbound conveyor.
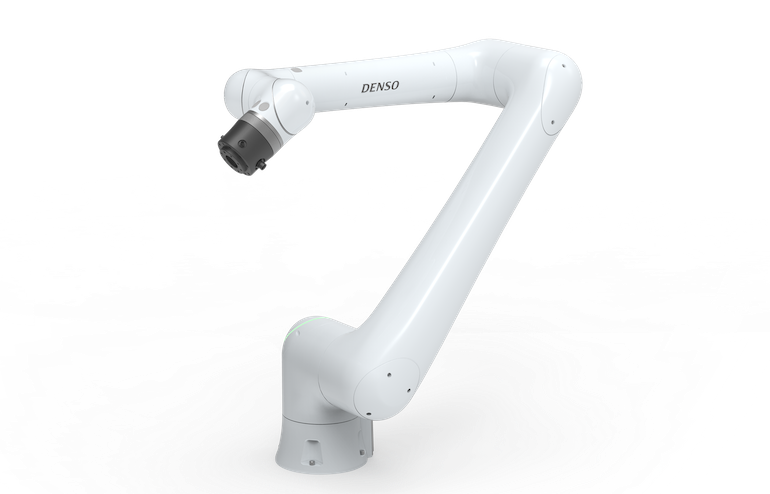
Determine 3: DENSO’s COBOTTA PRO 1300 collaborative robotic, for reference solely. Supply: Invent Automation
Companions deal with maneuverability, imaginative and prescient challenges
Exact actions alongside a number of axes are required for the robotic to select and place massive totes with out inflicting any collisions. The CapSen PiC 2.0 simulation atmosphere allowed the workforce to check the robotic’s maneuverability and guarantee every part was reachable and that the robotic wouldn’t collide with something.
However when the workforce examined the real-world system, it found that totes started to bend after they have been picked up by the robotic. To compensate for the tote’s weight and to make sure fluid movement with out collision throughout the compact cell, the companions labored to customise the system.
“We use AI in our software program to allow robots to carry out quite a lot of pick-and-place duties, together with random bin choosing, machine tending, packaging, meeting, and tote dealing with” mentioned Jared Glover, CEO of CapSen Robotics. “For difficult purposes, particularly these the place the simulation atmosphere alone gained’t suffice, we customise our AI algorithms and fashions primarily based on information from the manufacturing job. This allows the software program to optimize the movement of the robotic to permit it to maneuver freely with out collisions and to switch the tote throughout the cycle time.”
For DENSO’s tote-handling undertaking, CapSen Robotics first skilled its AI software program to detect and localize the tote’s deal with. The RGB-D digicam captures photographs of the deal with, and the software program runs machine studying algorithms that detect the deal with, permitting the software program to then do the movement planning for the robotic.
As soon as the robotic’s finish effector is positioned into the deal with, the load of the tote should be recognized so the robotic doesn’t cease working or make sudden jerk motions that trigger the tote to fall. As an alternative of utilizing a scale, CapSen’s software program analyzes the torque values on the motor and makes use of these values to find out the load for choosing.
“Utilizing the torque sensing of the robotic to acquire the load and naturally affirm that the tote was picked up was a worthwhile poka-yoke that CapSen added to the system,” mentioned Kevin Peek, manufacturing engineer at DENSO.
As well as, some machine imaginative and prescient challenges emerged through the design and set up of the system, however the collaborative workforce labored collectively to stop them from changing into a difficulty.
“Stacks of totes can even have as much as six totes in them, so the system wanted to make sure correct stacking,” in accordance with Peek. “If there are solely two totes, perhaps it’s much less of a difficulty, but when there are six totes stacked up and one just isn’t nested correctly, the entire stack may fall over and trigger a giant delay within the course of.”
To unravel this problem, the system is designed so that when a robotic units a tote onto a stack the robotic strikes backward barely to view the stack with the digicam. Machine studying algorithms within the software program helped the system to search for a niche between two totes and guarantee correct stacking, whereas the software program additionally counted and verified the right variety of totes within the stack.
Register immediately to save lots of 40% on convention passes!
DENSO stories zero drops, zero missed picks
Finally, the versality of the CapSen PiC 2.0 software program led to it being chosen because the software program resolution for this undertaking, because it permits finish customers to totally use all the information coming from the totally different items of system {hardware}. That is as a substitute of working via native programming, like when utilizing a programmable logic controller (PLC). On this software, there isn’t any PLC within the cupboard.

Determine 4: CapSen PiC’s intuitive HMI reveals system standing and makes the method of operating the operation easy. Supply: Invent Automation
The whole lot is dealt with within the CapSen human-machine interface (HMI). Operators can use it to manage machines, get hold of robotic calibration info, and visualize what the digicam sees, amongst different options (Determine 4).
The person interface was designed in order that non-technical staff are empowered to function the system as a part of their every day routines with out the necessity for automation or engineering experience.
The software program can be {hardware} agnostic, which offered a selected profit to DENSO. Actually, preliminary testing of the system concerned cell manipulation, the place an autonomous cell robotic (AMR) carried the robotic across the facility with the aim of shifting totes and different containers all through the warehouse.
On this configuration, CapSen’s software program controls the AMR, obtains coordinates from it, and sends correction directions to the AMR to line up the AMR to circulate rack lanes.
Whereas stacking and destacking totes is a typical software in industrial environments, this technique was designed with flexibility in thoughts, in order that it may be expanded or retrofitted to different purposes or made cell with an AMR.
As well as, for the reason that system was put in, the robotic has not dropped one tote or missed one decide, eradicating each a bodily and metaphorical weight from the shoulders of DENSO staff.
In regards to the writer
Bo Ridley is government vp at Knoxville, Tenn.-based Invent Automation. He beforehand labored as a manufacturing engineer and a machine designer at DENSO. This case research is posted with permission.